Table of Contents
- The Planning Gap in Modern Manufacturing
- Decoupled Systems, Decoupled Teams
- APS: Purpose Built for Complex Manufacturing
- Add the Right Tool to Your Manufacturing Toolbox
Ask anyone handling production planning in a complex manufacturing environment what their greatest obstacles to success are. If they’re being honest, you’ll probably hear common complaints like these:
“The organization is too siloed. Departments that should be working together don’t seem capable of collaborating.”
“Sales keeps promising delivery dates we can’t meet. I know we need to be competitive to win the order, but we can’t just conjure up capacity out of thin air.”
“We can’t seem to stick to the production schedule. Even when we think we’re being totally realistic, we still seem to find a way to miss delivery dates. It’s hurting our credibility with customers.”
While these may all sound like “people” complaints, the answer to these challenges does not lie in your human resources department.
In this post, we’re going to dive into why the software you use to manage your manufacturing production may lie at the root of your problem. The good news is that you don’t need to replace any of your people to turn things around. You don’t even need to replace your current systems. Like all production environments, you just need the right tool for the job.
The Planning Gap in Modern Manufacturing
When Materials Resource Planning (MRP) was introduced in the 1960’s it was heralded as the answer to solving the perennial problem of not having the right inventory available at the right time. Keep in mind that Just-in-Time replenishment and Lean Manufacturing principles were still just a twinkle in the eye of a couple of manufacturing engineers at Toyota in Japan. Manufacturers also had fewer challenges finding people that wanted to work in a factory, so people resources weren’t as constrained as they are today.
Advancements have been made, such as the integration of MRP into ERP. This eliminated some of the time-intensive, error-prone double entry bookkeeping that plagued manufacturers in the early days. Nevertheless, MRP systems still suffer from several critical shortcomings:
- MRP decouples supply and demand at every level in the bill of materials. Each level is kept in loose alignment based on the due date of the production order and the static lead time of the part. This decoupling causes the following issues in today’s manufacturing
- When MRP was first introduced, inventory was considered solely as an asset, the same as cash. Inventory could be used to buffer against this variability at every level of the bill of material, further decoupling the manufacturing process. Then Lean and JIT came along and taught manufacturers the real cost of inventory. As inventory was leaned out of the system, MRP became responsible for managing a level of variability and synchronization it was never designed to handle.
- Manufacturing environments are, by their nature, tightly coupled dynamic environments. MRP obfuscates this with no direct line of sight between a miss or delay at any lower-level purchase order or production order and the end customer order.
- Synchronization is envisioned as being carried out through approval of MRP action messages that redate the hundreds or thousands of decoupled production orders to bring their dates into alignment. I have yet to be in a manufacturing environment where production orders are kept in alignment using this process.
- MRP still assumes infinite capacity. Largely this means that MRP is producing an infeasible schedule without insights on where existing or emerging bottlenecks are within the production process. To learn how to address this challenge, check out our blog post on finite capacity planning.
- Since MRP does not consider resource capacity, it can do very little to help the manufacturer identify and manage capacity constraints. Without finite capacity planning, MRP is at odds with creating the pull-based manufacturing processes envisioned by methodologies like Theory of Constraints and Lean Manufacturing.
- MRP plans in daily buckets and often does not prioritize work on resources at any level lower than day. This further erodes MRP’s ability to synchronize operations in today’s manufacturing environments. Ensuring priority alignment between every step in the routing and every level in the bill of materials is critical to flow and throughput. MRP wasn’t designed for this reality and therefore can’t remain responsible for orchestrating today’s planning and scheduling.
The bottom line is that MRP systems were designed for manufacturing as it was 60+ years ago, not for the manufacturing of today. This is why most manufacturers today are using MRP to launch production orders and purchase orders, but are carrying out scheduling via spreadsheets. If you’re still using spreadsheets, you might want to go check out our 7 tips for moving away from them.
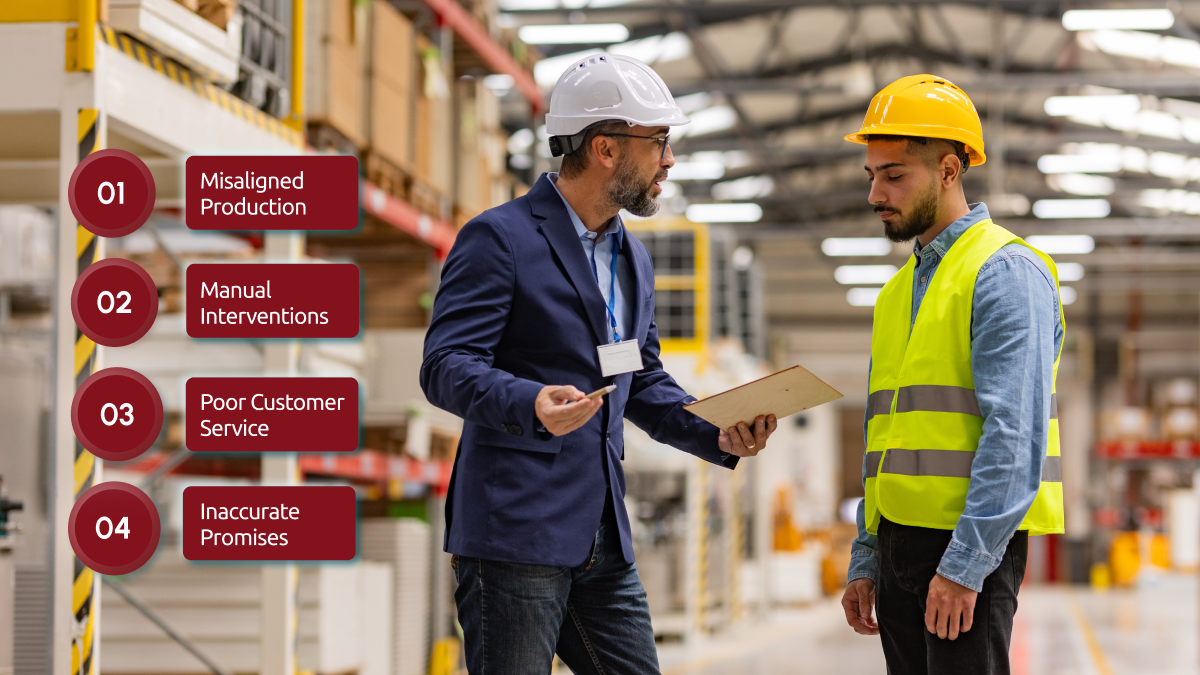
Decoupled Systems, Decoupled Teams
As anyone who has ever worked in manufacturing knows, collaboration between teams is critical. Even those who rarely set foot on the factory floor, such as your sales and customer service teams, need to be on the same page with production. Since MRP offers limited visibility into factory capacity or order progress, these silos cost the manufacturer time, money, and reputation. Here are a few examples of how lack of visibility creates chaos throughout the organization:
Misaligned Production – In dynamic markets, production priorities can change quickly, but MRP systems do very little to maintain alignment of priorities. Valuable time is lost as planners work to adapt schedules
Manual Interventions – If the change is significant, production teams may be asked to stop working to wait for the new orders. Downtime can cost manufacturers thousands of dollars per hour, but continuing to produce items that are no longer needed can be just as expensive. Once a new schedule is created, it must also be manually communicated to production teams so that work can be started again.
Poor Customer Service – As production disruptions and changing priorities impact the production schedule, it almost always causes some orders to slip. Customers may not find out about the delay until they call to check the status of their order after the delivery date has passed. While the delay might have been acceptable if they were informed ahead of time, they now have to adapt their plans to the new schedule on short notice.
Inaccurate Delivery Promises – Meanwhile, sales continues to provide delivery dates according to whatever standard lead times they were given. (Or based on what they think they need to promise to get the order.) At best, without visibility into capacity, they have no idea whether the promised dates can be met.
Some manufacturers try to break down silos with weekly or biweekly Sales and Operations planning meetings. These can be time-consuming, painful meetings. Worse yet, given the dynamic nature of complex manufacturing environments, any benefits are short-lived.
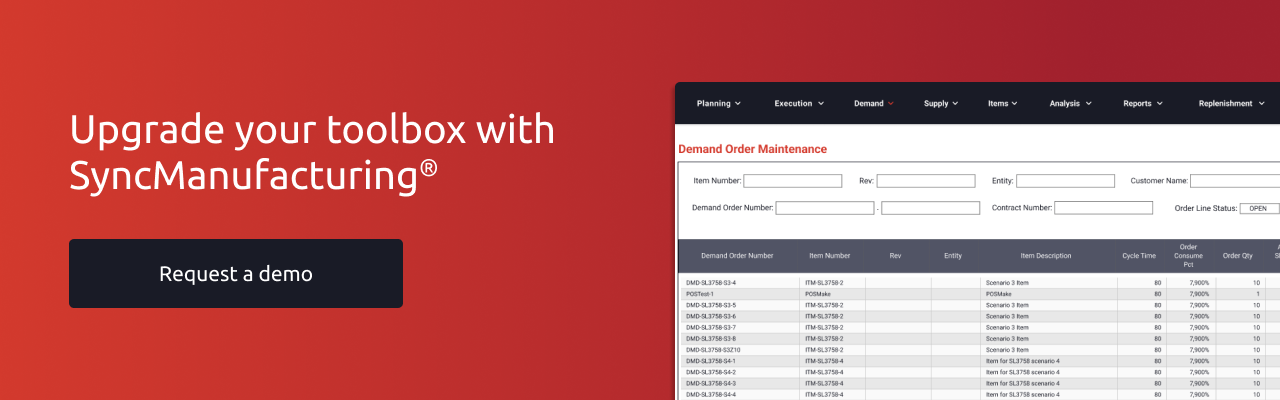
APS: Purpose Built for Complex Manufacturing
Advanced Planning and Scheduling systems (APS), like SyncManufacturing® from Synchrono®, are designed to help production planners and schedulers optimize production to meet demand. Unlike traditional MRP solutions, APS takes into consideration capacity constraints (also known as finite capacity planning) as well as inventory availability and dynamically calculated lead times – and in real time. This means sales knows what it can promise to customers. (No more excuses!)
When schedules change, SyncManufacturing automatically aligns all resources through every level of the bill of materials. The impact of the change is known to everyone in the environment. Operators always know the priority of the work assigned to them, production supervisors automatically know the urgency of work within cells. In addition, procurement knows any changes in priority they need to communicate to their suppliers and sales and customer service can proactively reach out to their customers if there is a positive or negative change to their expected delivery.
SyncManufacturing can also help production managers identify the real constraints in their production environment. These constraints can be leveraged using a patented scheduling algorithm called CONLOADTM to create the type of pull system envisioned in Theory of Constraints and Lean Manufacturing.
Finally, SyncManufacturing, through automated allocation processes, establishes the direct links and tight coupling between production orders at all levels of the bill of materials. This allocation brings the digital model in alignment with the highly connected manufacturing environments of today. The impact of a missed purchase order delivery or a machine breakdown is known instantly throughout the entire value stream allowing informed decision-making on how to resolve or clear visibility to inform the customer if a delivery will be missed.
Add the Right Tool to Your Manufacturing Toolbox
SyncManufacturing provides real-time integration into existing ERP systems, including MRP. So, as we said at the beginning of this post, manufacturers do not typically need to replace their current software, including their MRP systems, to take advantage of SyncManufacturing. Think of it as adding one tool to your toolbox that you never knew you always needed.
To learn more, reach out to us. You can contact us with questions or request a demo below.