Table of Contents
- The Difference Between ATP and CTP
- Why ATP Falls Short of CTP
- CTP Gives Manufacturers an Order Reservation System
- CTP Continually Monitors the Order Throughout Its Lifecycle
- Is Guesswork Good Enough for Your Manufacturing Operations?
With global competition intensifying, the number of manufacturers competing for your customers’ business is growing. So how does one create a sustainable advantage in a rapidly shifting competitive landscape? The answer lies in going back to one basic that was as true when the first manufacturer made the first widget as it is today: Deliver on your promises.
In this post, I’ll drill down into the one promise that still causes headaches for many manufacturers – on-time deliveries – and how the problem may not lie in your people or processes, but in the systems you use. In fact, one single feature can make a huge difference – whether you’re using ATP or CTP when making delivery commitments.
The Difference Between ATP and CTP
Most manufacturers have heard of the terms available to promise (ATP) and capable to promise (CTP). ERP solution vendors use them all the time. While they are sometimes used interchangeably, the difference between them is significant. To lay the groundwork, let’s start with some definitions. According to the Association for Supply Chain Management (ASCM):
- ATP is the uncommitted portion of a company’s inventory and planned production, maintained in the master schedule to support customer order promising.
- CTP is the process of determining if the required components and resources (e.g., materials, labor, machine capacity) are available to support a specific order or production request.
For me, the key difference stands out immediately. ATP refers to a thing (inventory), whereas CTP is a process. Put another way, ATP is exclusively inventory focused. It looks at what is currently available, either in inventory or in production, but not committed to another order. The difference is “available” for new orders. The available date for production or for orders in excess of inventory plus production is based on static lead times. It doesn’t matter if the plant has capacity or not, the answer is the same for ATP.
On the other hand, CTP looks at what could be, i.e., what could be promised to the customer based on the materials and resource capacity available. Instead of just promising whatever the customer asks for, CTP allows sales to provide a realistic availability based not just on inventory but also on factory capacity.
That’s a big difference!
Why ATP Falls Short of CTP
Leveraging CTP can help almost every manufacturer meet their customer commitments, but it’s particularly critical for complex manufacturers. Consider these shortfalls of ATP:
Static data – Because ATP looks only at inventory and static lead times, it doesn’t account for changes in demand, production delays, capacity changes, or resource constraints. The more overloaded and volatile the manufacturing environment, the less accurate the ATP answer will be. Static lead times are blind to capacity overloads and the actual volatility of the manufacturing environment.
No constraints management – ATP completely ignores production constraints. As much as we’d all like to believe constraints aren’t an issue, they are often the main issue in complex manufacturing environments.
Lack of real-time scheduling – As should be apparent, ATP is not tied to scheduling the way CTP is. As production schedules change, CTP information is automatically updated while ATP allows sales to continue to promise based on inventory alone. Often in ATP environments, customers aren’t notified an order is going to be late until the shipment has already been missed.
Overpromising – The bottom line is that trying to get by with ATP in a complex manufacturing environment can lead to missed customer commitments and poor customer service.
CTP Gives Manufacturers an Order Reservation System
In a CTP environment, every new order gets a capable date that is fully vetted for both capacity and material availability to ensure the quoted date is in perfect alignment with the manufacturer’s capabilities. Every time a new order is entered, it reserves its spot in the schedule and the materials it requires. This ensures that capacity is not oversold. It ensures that the manufacturer can provide a reliable delivery date with confidence to their customer.
Since this is an automated process, environments with CTP drastically reduce the churn between sales and production. Sales isn’t constantly contacting production to know what can be delivered and production isn’t constantly going through manual calculations to try and determine what can be delivered. The only time production needs to get involved is when a customer’s request date cannot be made.
Provided the CTP system communicated the capacity and material constraints for the order, production knows the dials that must be turned to improve the date. Can they run overtime, can they expedite a purchased part, can they slide another order to make room, etc. CTP allows the manufacturer to be proactive. CTP provides all the necessary information up-front to make the best decisions for the manufacturer and their customers.
CTP Continually Monitors the Order Throughout Its Lifecycle
Unlike ATP, CTP accounts for the real-time conditions of the production environment. By continuously establishing a schedule based on the current state of the manufacturing plant along with capacity and materials availability, the CTP is always reflecting the projected delivery date of every order in the system. CTP keeps the manufacturer in proactive mode, eliminating the guesswork and the manual intervention.
In cases where a drastic event like a multi-day machine breakdown, a material showing up from the supplier week(s) late, or major components of the build needing to be scrapped, CTP allows the manufacturer to proactively communicate with their customer. The manufacturer can let their customer know as soon as they know that an order is at risk and will be armed with a new CTP date to provide the customer again fully vetted against the state of manufacturing along with its capacity and material availability.
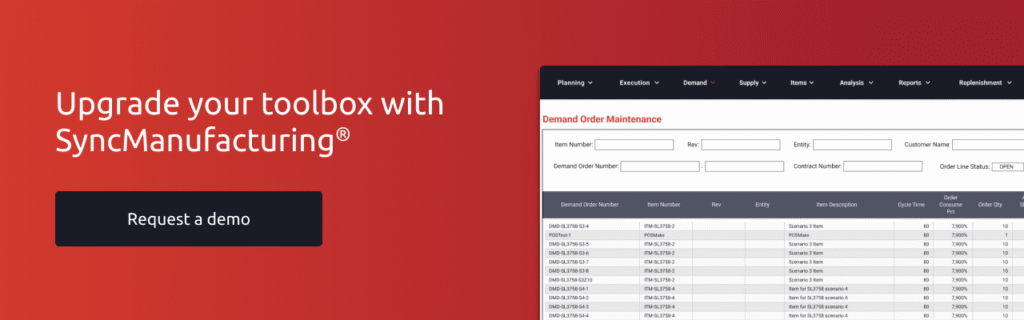
Support Best Practices
CTP even aligns to lean manufacturing and waste reduction initiatives by allowing manufacturers to align production to actual demand, reducing overproduction, scrap, excess inventory, and operational waste.
Is Guesswork Good Enough for Your Manufacturing Operation?
Probably not. Unfortunately, many commercial ERP software applications only offer ATP functionality, requiring sales and production managers to make their “best guess” at what can be delivered by when. These systems simply aren’t designed for complex manufacturing environments where capacity constraints are the limiting factor, production priorities can change at a moment’s notice, and meeting customer commitments is critical to long-term business success.
That’s why SyncManufacturing from Synchrono provides CTP functionality that can be used with your existing ERP system to help you:
- Commit to orders with confidence
- Adjust to supply chain disruptions
- Reprioritize production easily and as needed
- Manage constraints to increase throughput
- Improve on-time deliveries
- Control the chaos
If guesswork isn’t good enough for you, reach out to learn more or schedule a demo and see SyncManufacturing in action.